What Makes Our Stainless Steel Manifolds Stand Out: MarineTorq’s R&D Journey
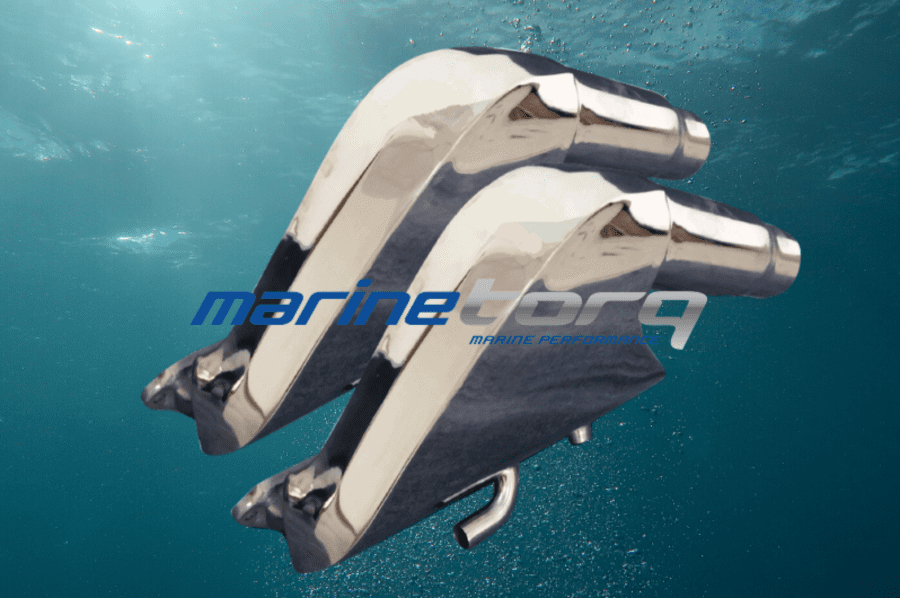
The MarineTorq product has evolved significantly over the years. Here is an insight into some of these changes…
Anti-Water Reversion Design
All MarineTorq Stainless Steel manifolds now include an anti-water reversion cone- an innovative design which offers complete peace of mind.
So what is water reversion? In simple terms, it’s a cam overlap (or vacuum effect) created by an engine’s exhaust pulses, which can suck the manifold’s cooling water back into the engine. Getting water in your engine is never a good idea, which is why it’s critical to keep exhaust gases and water separate until they exit the riser. If water does enter the gas chamber of a manifold, it can cause extensive rusting or hydrolock, in which case you’re usually looking at irreparable damage, engine failure, and a hefty bill.
By redesigning the exhaust gas outlet, a MarineTorq manifold stabilises the exhaust flow as it exits, and prevents any water from being sucked back into the engine. Note an anti-water reversion cone will not stop water entering the engine if a boat is not handled correctly, such as raising the static water line from too much weight aft, or chopping the throttle at high speeds.
Steel Grade
When tossing up between cast iron or stainless steel, one of the most common assumptions is that stainless steel becomes brittle and is prone to rust. Don’t be fooled- not all grades of steel are alike, and that’s why a manifold made with the wrong grade of steel can easily give stainless steel a bad name.
MarineTorq has extensively tested varying grades of steel to determine the best material for marine applications. Designed to withstand cracking, corrosion and extreme heat, the stainless steel used in our manifolds is additionally MIG welded (for optimum strength) and TIG welded (the two welded surfaces are melted together.)
In accord with MarineTorq’s ISO9001 accreditation, all stainless steel is routinely checked and tested a further 2-4 times after each manifold has been manufactured.
Learn more about stainless steel and its benefits compared to cast iron here.
Steel Thickness
One of the many advantages of stainless steel is its strength to weight advantage over other materials.
Cast iron manifolds have extremely thick walls to slow down the corrosion process, and as a result often weigh upwards of 50kg. Stainless steel is an excellent alternative to cast iron, as even with a 2mm wall thickness like on MarineTorq manifolds, it is still lightweight and can save up to 80% in dead weight.
At MarineTorq, 2mm steel is used in both the manifold itself plus the outer water jacket, and is regularly measured and checked according to ISO9001 standards. Compared to thinner steel which is more prone to cracking and rusting, 2mm thick stainless steel can withstand extreme heat and pressure, and handle up to 650-700 horsepower. For a behind the scenes look at MarineTorq’s manufacturing process, check out our water pressure testing in action on this set of manifolds for a GM LS small block engine.
MarineTorq can also customise manifolds to accommodate extra power, such as this twin turbo set up at 1000HP on a customer’s 455 Oldsmobile. To discuss your custom requirements, contact us here.
Maintenance Intervals
Ask any customer why they replaced their OEM manifolds with stainless steel, and one of their top reasons will likely be they were sick of constantly replacing their cast iron manifolds.
Straight off the bat, stainless steel offers a much longer lifespan than cast iron. At MarineTorq, we offer a 10 year warranty across the majority of our range, however we have known stainless steel manifolds to still be going strong after 20 years of saltwater use.
Compare this to cast iron manifolds, which can have a lifespan as short as 2-3 years. Frequent replacements are inconvenient, and the costs can add up over time. Ultimately, you end up spending more time in the workshop, and with the worry of what is essentially a ticking time bomb in your engine bay.
If the prospect of getting so many years out of your manifold doesn’t already excite you enough, our stainless steel manifolds can also give you total peace of mind from corrosion and manifold failure. The only maintenance needed to prevent rusting is an anode replacement, which we recommend doing twice a year.
Sacrificial anodes have always been an integral part of MarineTorq’s manifolds, however older designs included two smaller anodes. This meant checking and replacing every 3 months to maintain the condition and warranty of the manifold.
To reduce maintenance intervals, now each manifold includes just the one, much larger anode. As a result, the anode lasts for longer, and the single replacement is only required every 6 months, instead of 4 times a year. Find out more information on MarineTorq’s zinc anodes here.
To find a solution for your boat, fill out the below form and one of the team will be in touch.